For Lochinvar boiler troubleshooting, first, check for error codes on the display panel. Then, ensure the power supply is stable and functional.
Lochinvar boilers are known for their reliability and efficiency, but occasional issues can arise. Proper troubleshooting is essential to maintain optimal performance and avoid costly repairs. Common problems include ignition failures, temperature inconsistencies, and pressure issues. Identifying error codes on the display panel can provide insights into the specific problem.
Regular maintenance, such as cleaning filters and checking connections, can prevent many issues. For more complex problems, consulting the user manual or contacting a professional technician is advisable. Proper care and timely troubleshooting can extend the lifespan of your Lochinvar boiler and ensure consistent heating.
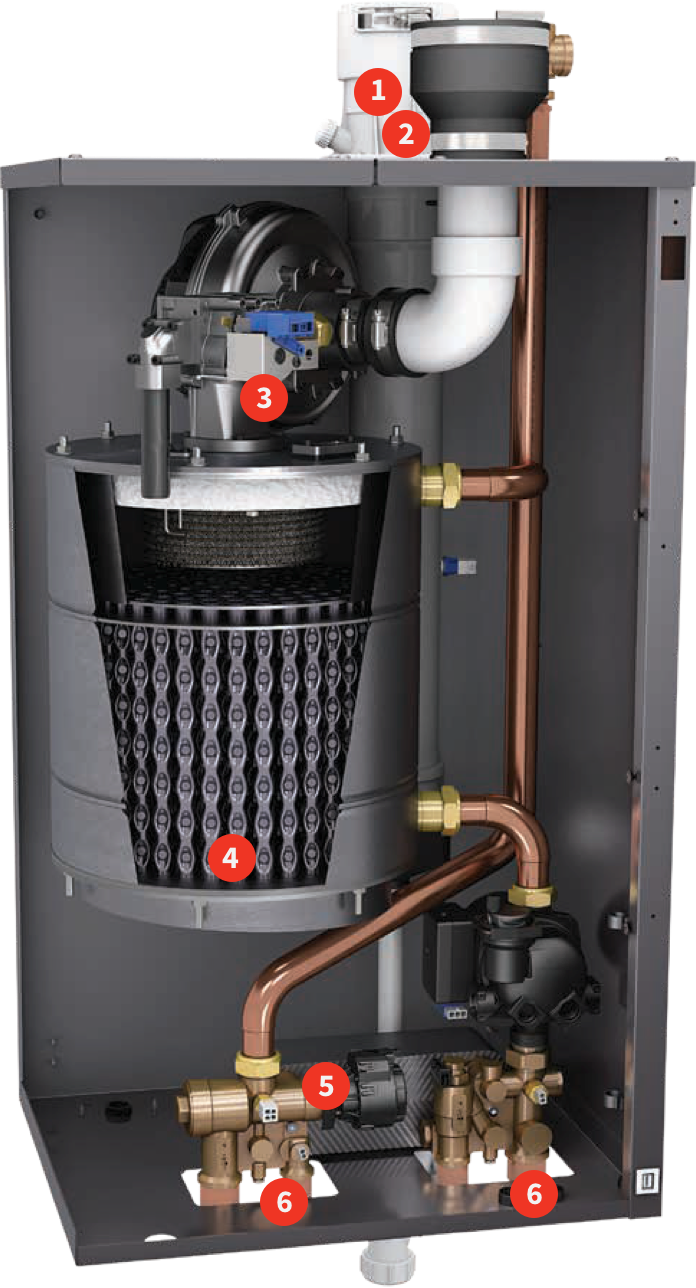
Credit: www.lochinvar.com
Introduction To Lochinvar Boilers
Lochinvar boilers are known for their reliability and efficiency. They are a top choice for many. These boilers come in different models, each designed for specific needs. Whether for residential or commercial use, Lochinvar has a boiler for you.
Why Choose Lochinvar?
Lochinvar boilers offer many benefits. Here are some reasons why they stand out:
- Energy Efficiency: They save on energy costs.
- Durability: Built to last for years.
- Advanced Technology: Features like smart control systems.
- Environmentally Friendly: Low emissions and eco-friendly designs.
Common Applications
Lochinvar boilers are versatile. Here are some common uses:
- Residential Heating: Ideal for home heating solutions.
- Commercial Buildings: Perfect for offices and retail spaces.
- Industrial Use: Suitable for factories and manufacturing units.
- Hot Water Supply: Provides hot water for various needs.
Understanding the applications of Lochinvar boilers helps you choose the right model. They are an excellent investment for any setting.
Identifying Common Problems
Lochinvar boilers are known for their efficiency and reliability. Yet, they can sometimes run into issues. Identifying common problems early can save time and money. This guide will help you understand frequent error codes and typical symptoms of Lochinvar boilers.
Frequent Error Codes
Lochinvar boilers display error codes to identify issues. Knowing these codes helps in quick troubleshooting.
Error Code | Description |
---|---|
ERR 01 | High Limit Fault |
ERR 02 | Low Water Pressure |
ERR 03 | Ignition Failure |
ERR 04 | Flame Failure |
ERR 05 | Fan Speed Error |
Typical Symptoms
Several symptoms can indicate problems with your Lochinvar boiler. Identifying these symptoms can help in quick resolution.
- No Heat or Hot Water: Often due to low pressure or thermostat issues.
- Strange Noises: Could be air in the system or a faulty pump.
- Water Leaks: Usually caused by a broken seal or valve.
- Pilot Light Issues: The pilot light keeps going out or won’t light.
- Pressure Drop: A leak or a faulty pressure relief valve may be the cause.
By understanding these common problems, you can maintain your Lochinvar boiler efficiently.
Basic Troubleshooting Steps
Troubleshooting your Lochinvar boiler can be simple with basic steps. These steps can help identify common problems.
Initial Checks
Start with basic checks to ensure the boiler is functioning.
- Power Supply: Check if the boiler is getting power.
- Thermostat: Ensure the thermostat is set correctly.
- Pressure Levels: Verify that the water pressure is within the recommended range. The ideal pressure is usually between 1.0 and 2.0 bar.
- Fuel Supply: Ensure gas or oil supply is on and not interrupted.
Resetting The Boiler
Sometimes, a simple reset can solve minor issues. Follow these steps to reset:
- Locate the reset button on the boiler.
- Press and hold the button for 3-5 seconds.
- Wait for the boiler to restart.
- Check if the issue is resolved. If not, repeat the process.
After resetting, monitor your boiler to ensure it operates correctly. If problems persist, consider consulting a professional.

Credit: www.youtube.com
Addressing Ignition Failures
Ignition failures in Lochinvar boilers can be frustrating. This section will help you understand and fix these issues. We’ll explore common causes and provide solutions.
Causes Of Ignition Issues
Several factors can cause ignition failures in Lochinvar boilers. Identifying the root cause is the first step.
- Faulty Igniter: The igniter might be worn out or broken.
- Gas Supply Problems: Insufficient gas can prevent ignition.
- Blocked Burner: Dirt or debris can block the burner.
- Electrical Issues: Faulty wiring can disrupt ignition.
- Control Module Failure: The control module might be malfunctioning.
Solutions For Ignition Failures
Once you know the cause, you can apply the right solution.
- Replace the Igniter:
Inspect and replace the igniter if damaged. Use a multimeter to check for continuity.
- Check Gas Supply:
Ensure gas valves are open and the supply is adequate. Call your gas provider if needed.
- Clean the Burner:
Remove dirt or debris from the burner. Use a soft brush for cleaning.
- Inspect Electrical Connections:
Check all wiring and connections. Tighten any loose connections and replace damaged wires.
- Test the Control Module:
Use diagnostic tools to test the control module. Replace it if it’s faulty.
Problem | Solution |
---|---|
Faulty Igniter | Replace the igniter |
Gas Supply Problems | Check and ensure gas supply |
Blocked Burner | Clean the burner |
Electrical Issues | Inspect and repair wiring |
Control Module Failure | Test and replace control module |
Handling Temperature Fluctuations
Experiencing temperature fluctuations with your Lochinvar boiler can be frustrating. Ensuring consistent heating is crucial for comfort and efficiency. Let’s dive into common issues and solutions.
Inconsistent Heating
Inconsistent heating is a common problem with boilers. This can result in some rooms being too hot and others too cold. This inconsistency can be due to various factors.
- Check if the radiators are balanced.
- Ensure there are no airlocks in the system.
- Inspect the boiler’s pressure levels.
Balancing radiators involves adjusting the valves to ensure even heat distribution. Airlocks can be removed by bleeding the radiators. Low pressure can be fixed by adding water to the system.
Thermostat Issues
A faulty thermostat can cause temperature fluctuations. If the thermostat is not working, the boiler won’t heat effectively.
Problem | Solution |
---|---|
Thermostat not responding | Check batteries and connections. |
Incorrect temperature reading | Recalibrate or replace the thermostat. |
Ensure the thermostat is in a good location. Avoid placing it near heat sources or draughts. This placement ensures it reads the room’s temperature accurately.
By addressing these issues, you can handle temperature fluctuations effectively. A well-maintained boiler ensures a comfortable and warm home.
Dealing With Water Leaks
Water leaks in a Lochinvar boiler can cause serious issues. They can lead to water damage, higher utility bills, and reduced efficiency. Addressing leaks quickly is crucial to maintaining your boiler’s performance.
Identifying Leak Sources
Finding the source of the leak is the first step. Here are common areas to check:
- Pipes and Connections: Inspect all pipe joints and connections.
- Pressure Relief Valve: Look for leaks around the valve.
- Heat Exchanger: Check for signs of corrosion or cracks.
Use a flashlight to spot water droplets or damp areas. Sometimes, a leak might be tiny and hard to see.
Fixing Common Leaks
Once you identify the source, you can fix the leak. Here are some steps for common fixes:
- Pipes and Connections: Tighten any loose connections. Replace damaged pipes or seals.
- Pressure Relief Valve: If the valve is faulty, replace it. Ensure the new valve is properly installed.
- Heat Exchanger: For minor cracks, use an appropriate sealant. For major damage, consider replacing the heat exchanger.
Regular maintenance can prevent many leaks. Check your boiler periodically for any signs of wear and tear.
Here’s a quick summary of common leak sources and fixes:
Leak Source | Common Fix |
---|---|
Pipes and Connections | Tighten or replace |
Pressure Relief Valve | Replace faulty valve |
Heat Exchanger | Seal minor cracks or replace |
Maintaining Boiler Efficiency
Maintaining boiler efficiency is crucial for both performance and cost-effectiveness. A well-maintained boiler uses less energy and lasts longer. Below are tips to keep your Lochinvar boiler running efficiently.
Routine Maintenance Tips
Regular checks help prevent major issues. Here are some routine maintenance tips:
- Check Pressure Levels: Ensure the boiler pressure is within the recommended range.
- Inspect for Leaks: Look for any water or gas leaks around the boiler.
- Clean Heat Exchanger: Remove any dust or debris from the heat exchanger.
- Test Safety Valves: Ensure safety valves are functioning correctly.
- Monitor Thermostat: Check that the thermostat is accurate and responsive.
Importance Of Regular Servicing
Regular servicing is vital for the longevity of your Lochinvar boiler. It ensures all components are in good condition. Here are the benefits:
- Enhanced Efficiency: Regular servicing keeps the boiler running smoothly.
- Cost Savings: Efficient boilers consume less energy, reducing bills.
- Safety: Regular checks ensure there are no dangerous issues.
- Extended Lifespan: Well-maintained boilers last longer and perform better.
Here’s a quick reference table for maintenance activities:
Maintenance Task | Frequency |
---|---|
Check Pressure Levels | Monthly |
Inspect for Leaks | Monthly |
Clean Heat Exchanger | Annually |
Test Safety Valves | Annually |
Monitor Thermostat | Monthly |
Keeping up with these tasks helps maintain your boiler’s efficiency. A little effort goes a long way in ensuring a reliable and efficient heating system.
Credit: www.plumbingzone.com
When To Call A Professional
Lochinvar boilers are reliable, efficient, and durable. But like any machine, they need occasional troubleshooting. Knowing when to call a professional can save you time and money. This guide will help you identify the right moments to seek expert assistance.
Signs You Need Expert Help
Some signs indicate a need for professional intervention. Here are a few:
- Unusual noises: If your boiler makes strange sounds, call a technician.
- Frequent shutdowns: Frequent on-off cycles can signal serious issues.
- Water leaks: Leaks can cause significant damage. Get expert help.
- Low heat output: Inadequate heating might mean a deeper problem.
- Error codes: Error codes need professional diagnosis and repair.
Choosing The Right Technician
Selecting the right technician ensures your boiler works efficiently. Consider these tips:
- Certifications: Ensure the technician has proper certifications.
- Experience: Look for technicians with Lochinvar boiler experience.
- Reviews: Check online reviews and testimonials.
- Warranty: Verify if they offer service warranties.
- Response time: Fast response is crucial for urgent issues.
Criteria | Importance |
---|---|
Certifications | High |
Experience | High |
Reviews | Medium |
Warranty | Medium |
Response Time | High |
By following these guidelines, you can ensure your Lochinvar boiler stays in top shape.
Frequently Asked Questions
How Do I Reset My Lochinvar Boiler?
To reset your Lochinvar boiler, locate the reset button. Press and hold it for a few seconds. If the problem persists, consult your boiler manual or contact a professional technician.
Why Is My Lochinvar Boiler Not Heating?
If your Lochinvar boiler isn’t heating, check the thermostat settings first. Ensure the boiler is receiving power. If the issue continues, you may need professional assistance to diagnose and fix the problem.
What Causes A Lochinvar Boiler To Lockout?
A Lochinvar boiler lockout can be caused by various issues. Common reasons include low water pressure, ignition failure, or a faulty component. Refer to the error code displayed or consult a professional for a precise diagnosis.
How Often Should I Service My Lochinvar Boiler?
You should service your Lochinvar boiler annually. Regular maintenance ensures optimal performance, efficiency, and safety. It also helps prevent potential issues and prolongs the lifespan of your boiler.
Conclusion
Mastering Lochinvar boiler troubleshooting can save time and money. Regular maintenance keeps your system efficient. Address issues promptly to prevent bigger problems. Use our tips to enhance your boiler’s performance. Stay proactive and ensure a warm, comfortable home. Your heating system will thank you for the care.