### Shark Steam Mop Troubleshooting Ensure the water tank is full and securely attached. Check if the steam nozzle is clogged and clean it.
### Introduction Shark steam mops are popular for their efficiency in cleaning floors. They offer a chemical-free way to tackle dirt and grime. Despite their reliability, users may encounter issues. Troubleshooting common problems helps restore the mop’s functionality. Addressing minor issues can save time and prevent further damage.
Most problems stem from clogged nozzles or empty water tanks. Regular maintenance is key to prolonging the mop’s lifespan. Proper care includes cleaning the nozzle and checking water levels. Users can often resolve issues quickly and easily. This guide provides practical solutions for common Shark steam mop problems.
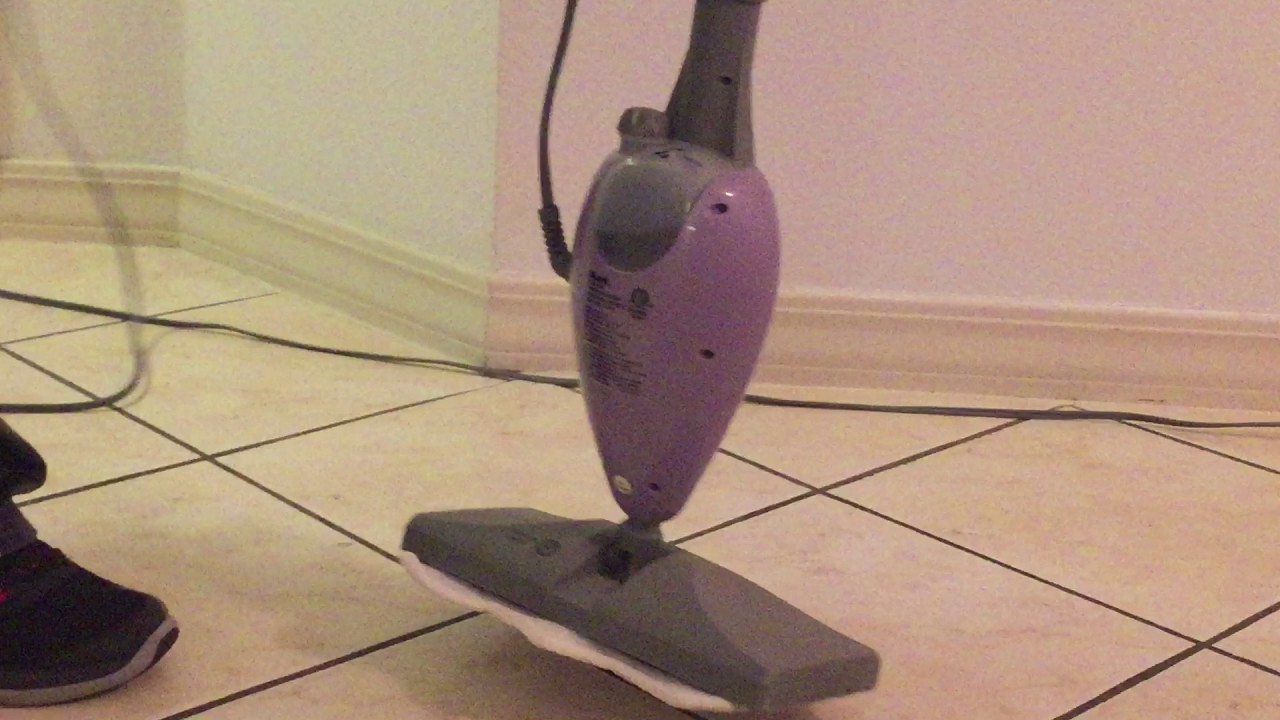
Credit: www.youtube.com
Introduction To Shark Steam Mops
Shark Steam Mops are popular for cleaning floors efficiently. They use steam to sanitize surfaces without chemicals. This makes them eco-friendly and safe for homes with kids and pets.
Benefits Of Using Steam Mops
Steam mops offer many benefits for cleaning your home:
- Sanitize Surfaces: Steam kills 99.9% of germs and bacteria.
- Chemical-Free Cleaning: No harsh chemicals, just water.
- Quick Drying: Floors dry quickly after mopping.
- Versatile: Suitable for various floor types like tiles, wood, and laminate.
- Effortless Cleaning: Steam loosens dirt, making it easy to wipe away.
Common Issues Encountered
Despite their benefits, Shark Steam Mops can have issues. Here are some common problems:
Issue | Possible Causes | Solutions |
---|---|---|
No Steam Production | Water tank empty, or clogged nozzle | Refill tank, clean nozzle |
Low Steam Output | Mineral buildup, or low water level | Descale unit, refill water |
Streaky Floors | Dirty mop pad, or hard water | Change pad, use distilled water |
Leaking Water | Overfilled tank, or damaged gasket | Empty some water, replace gasket |
Credit: www.ifixit.com
Steam Mop Not Turning On
Your Shark Steam Mop is a reliable cleaning tool. But sometimes, it may not turn on. This can be frustrating. Troubleshooting is necessary to identify the issue. Below are some steps to help you.
Power Supply Check
First, ensure the power supply is working. Check if the outlet has power. Plug another device into the outlet. If it works, the issue may be elsewhere. Also, make sure the mop is properly plugged in.
Try a different outlet if needed. Sometimes, the outlet may be faulty. It’s a simple step but often overlooked.
Fuse And Circuit Breaker
Next, check the fuse in the plug. Unplug the steam mop first. Then, open the plug and inspect the fuse. If it’s blown, replace it with a new one. Fuses are inexpensive and easy to find.
Also, check the circuit breaker in your home’s electrical panel. Sometimes, a tripped breaker can cause power issues. Reset the breaker if needed. Make sure all connections are secure.
Below is a table to help you with the steps:
Step | Action |
---|---|
1 | Check the power outlet with another device. |
2 | Ensure the steam mop is properly plugged in. |
3 | Inspect and replace the fuse if needed. |
4 | Reset the circuit breaker if it’s tripped. |
By following these steps, you can identify and fix the issue. Remember, always unplug the device before inspecting it. Safety first!
No Steam Production
Shark steam mops are popular for their efficiency and ease of use. But users sometimes face an issue: No Steam Production. This problem can be frustrating but can often be resolved with a few simple steps. Below, we explore common causes and solutions.
Water Tank Inspection
The first step in troubleshooting is the Water Tank Inspection. Ensure the water tank is filled with clean, distilled water. This prevents mineral buildup that can block steam production.
- Remove the water tank from the mop.
- Check if the tank is empty or low on water.
- Fill the tank with distilled water to the recommended level.
- Securely reattach the tank to the mop.
If the tank is full and the mop still produces no steam, inspect the tank for any cracks or leaks. A damaged tank cannot maintain the pressure needed for steam production.
Steam Nozzle Blockage
A common reason for no steam production is a Steam Nozzle Blockage. Dirt and mineral deposits can clog the nozzle, preventing steam from escaping.
- Turn off the mop and unplug it from the power source.
- Allow the mop to cool down completely.
- Use a paperclip or a small pin to gently clear the nozzle.
- Insert the pin into the nozzle hole and move it around to dislodge any blockages.
After clearing the nozzle, plug the mop back in and test for steam production. If the steam flow is restored, regular cleaning of the nozzle can prevent future blockages.
Regular maintenance can keep your Shark steam mop working efficiently. By inspecting the water tank and cleaning the steam nozzle, you can often resolve steam production issues quickly.
Poor Steam Output
A common issue with Shark steam mops is poor steam output. This problem can make your cleaning tasks less effective. Below are some troubleshooting steps to address this issue.
Water Quality Issues
Using tap water can lead to mineral buildup. This buildup can block steam production. It’s best to use distilled water. Distilled water reduces the risk of clogs and ensures smooth operation.
- Empty the water tank after each use.
- Refill with fresh distilled water before every cleaning session.
- Avoid using hard water to prevent mineral deposits.
Cleaning The Heating Element
Mineral deposits can also form on the heating element. This can restrict steam flow. Regular cleaning of the heating element helps maintain optimal performance.
- Unplug the steam mop and let it cool down.
- Remove the water tank.
- Use a vinegar solution to clean the heating element.
- Fill the tank with a 50/50 mix of vinegar and water.
- Run the mop until the tank is empty.
- Rinse the tank thoroughly with distilled water.
Perform this cleaning routine once a month. This ensures your steam mop stays efficient and effective.
Issue | Solution |
---|---|
Mineral Buildup | Use distilled water |
Clogged Heating Element | Clean with vinegar solution |
Mop Leaving Streaks
Is your Shark Steam Mop leaving streaks? This can be frustrating. Streaks can make your floors look dirty. Here are some tips to fix this issue.
Using Distilled Water
Tap water can contain minerals that leave streaks. To avoid this, use distilled water. Distilled water is free from minerals. This helps prevent streaks on your floors.
Follow these steps for using distilled water:
- Empty the water tank of any tap water.
- Fill the tank with distilled water.
- Use the steam mop as usual.
Using distilled water can make a big difference. It helps keep your floors streak-free.
Proper Cleaning Techniques
Using the right cleaning techniques is important. Here are some tips:
- Move the mop slowly and steadily.
- Avoid using too much steam.
- Change the mop pad often.
Changing the mop pad is key. A dirty pad can leave streaks. Keep extra pads handy and switch them out as needed.
Issue | Solution |
---|---|
Mineral buildup | Use distilled water |
Dirty mop pad | Change the pad often |
Excess steam | Use less steam |
By following these tips, your Shark Steam Mop should leave your floors clean and streak-free.
Credit: www.ifixit.com
Mop Pad Not Attaching
Is your Shark Steam Mop pad not attaching properly? This issue can hinder your cleaning routine. Let’s explore some troubleshooting steps to fix this common problem.
Inspecting Pad Attachment
First, check if the mop pad is aligned correctly with the mop head. Ensure all corners and edges match perfectly. A misaligned pad won’t attach securely.
Next, inspect the Velcro strips on the mop head. Dirt or debris can affect attachment. Clean the Velcro strips using a brush or cloth. This helps the mop pad stick better.
Also, examine the mop pad itself. Over time, wear and tear can reduce its grip. Look for any damage or excessive wear on the pad.
Replacing Mop Pads
If the mop pad is worn out, consider replacing it. Using a new pad can solve attachment issues.
- Purchase genuine Shark replacement pads.
- Follow the instructions on the packaging for proper installation.
- Ensure the new pad aligns perfectly with the mop head.
Using high-quality replacement pads ensures better performance and longevity.
Remember, regular maintenance of your Shark Steam Mop is essential. Keep the Velcro strips clean and replace worn-out pads promptly. This guarantees efficient cleaning every time.
Strange Noises
Shark steam mops are effective cleaning tools. Sometimes, they make strange noises. These noises can disrupt your cleaning routine. Understanding and fixing these noises is essential for optimal performance.
Checking For Obstructions
Strange noises often come from obstructions. Check the water tank first. Make sure it is clean and free of debris. Look at the steam nozzle as well. Debris can block the nozzle and cause noises.
Use a needle to clear any blockages in the nozzle. Check the mop head for tangled hair or fibers. Remove any obstructions you find.
Inspecting Internal Components
If the noise persists, inspect internal components. Unplug the mop before starting. Remove the water tank and inspect the heating element. Look for signs of damage or corrosion.
Next, check the steam hose. Ensure it is not kinked or damaged. Any damage to internal parts can cause strange noises. Replace damaged parts if necessary.
Lastly, check the motor. If the motor is making unusual sounds, it may need professional service. Always consult the user manual for guidance.
Handle And Movement Issues
Shark steam mops are fantastic for keeping floors clean. But sometimes, you might face issues with the handle or movement. This section will help you fix those problems.
Handle Tightening
If the handle feels loose, it can affect your cleaning. Follow these steps to tighten the handle:
- Turn off and unplug the steam mop.
- Locate the screws on the handle.
- Use a screwdriver to tighten these screws.
Make sure the handle is secure. A loose handle can lead to poor cleaning. Tightening the handle is an easy fix. It helps maintain the mop’s performance.
Wheel And Swivel Maintenance
Wheels and swivels help the mop move smoothly. If they get stuck, cleaning becomes hard. Here’s how to keep them in good shape:
- Check the wheels: Make sure they spin freely.
- Clean any debris: Remove hair and dirt from wheels.
- Lubricate: Use a small amount of silicone spray.
For the swivel part, ensure it moves without resistance. If it feels stiff, apply a bit of silicone spray. Regular maintenance prevents movement issues. It extends the life of your steam mop.
Frequently Asked Questions
Why Is My Shark Steam Mop Not Putting Out Steam?
Your Shark steam mop may not produce steam due to clogged nozzles, insufficient water, or a malfunctioning heating element. Ensure proper water levels and clean the nozzles. If the problem persists, consult the user manual or seek professional repair.
How Do I Fix My Steam Mop Not Steaming?
Check the water tank for clogs. Ensure it’s filled with clean water. Clean the steam nozzle and vents. Check the power cord connection.
How Do I Unblock My Steam Mop?
Unplug the steam mop and let it cool down. Remove and clean the nozzle with a paperclip. Refill the water tank.
Why Is The Light Blinking On My Shark Steam Mop?
The light on your Shark steam mop blinks due to low water levels or a clogged nozzle. Refill the tank and check for blockages.
Conclusion
Maintaining your Shark steam mop ensures optimal performance and longevity. Follow the troubleshooting tips for a hassle-free cleaning experience. Regular maintenance can prevent common issues, saving time and money. Enjoy a spotless home with minimal effort by keeping your steam mop in top condition.
Your floors will thank you!